Как собирают самолеты The Village побывал на заводе Airbus в Германии и узнал, как делают популярные серии A320 и A320neo
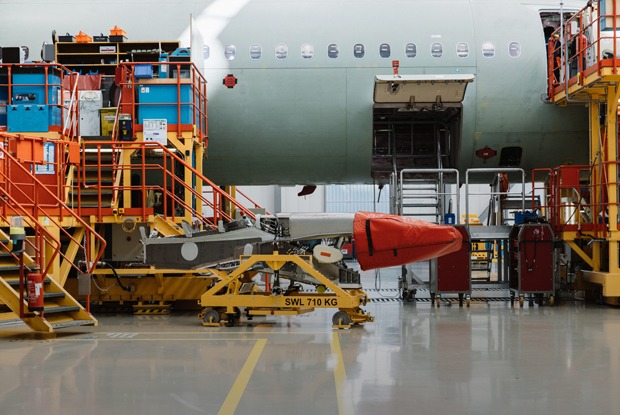
Сейчас примерно каждые полсекунды в мировых аэропортах взлетает или садится один из самолетов марки Airbus. Сама компания появилась 50 лет назад как европейский конкурент авиаконцернам из США, но самолеты здесь решили делать по принципиально новой схеме — их не собирали от начала до конца на одном заводе, а разделили производство между несколькими городами. В каждом из них выпускали свою часть (например, секцию фюзеляжа или крыло), а затем свозили их на завод, где все собирали вместе, как большой конструктор. Сейчас производство Airbus по-прежнему разделено между несколькими странами, а к европейским добавились еще и заводы в Канаде, США и Китае. Мы побывали на одной из линий финальной сборки Airbus в Гамбурге во время передачи сотого самолета для авиакомпании S7 Airlines и узнали, почему на производстве предпочитают ручной труд, из чего сделаны самые прочные части самолета и зачем на кресло пилота кладут овечью шкуру.
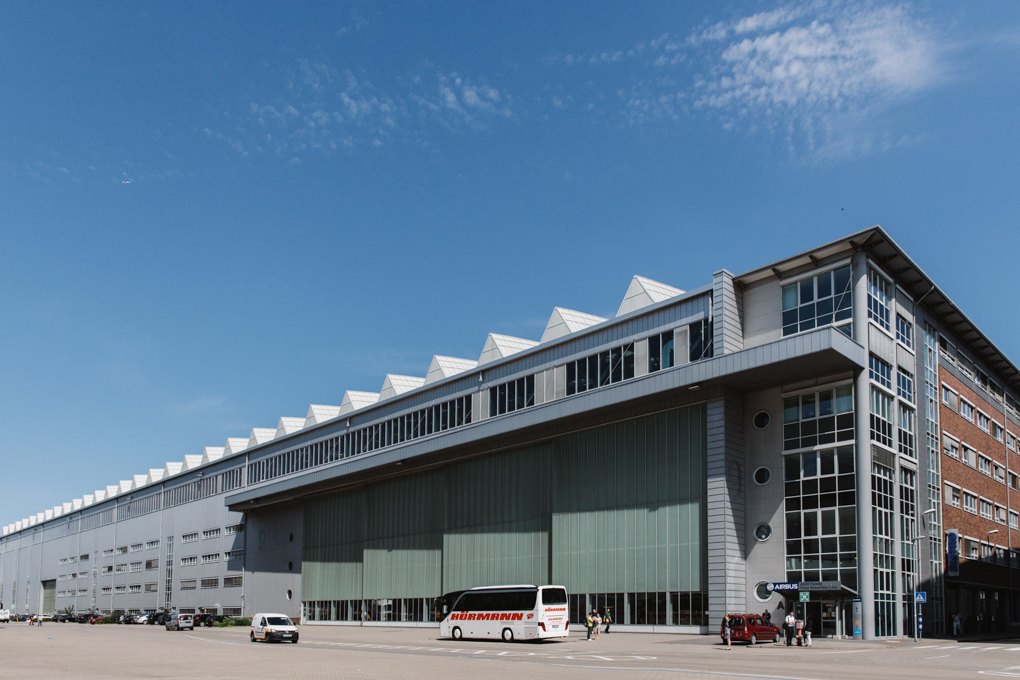
Завод и штаб-квартира
Местоположение: Гамбург, Германия
Территория: 3,5 квадратного километра
Количество рабочих: 13 000 человек
4 сборочные линии
30 самолетов разных моделей в месяц
В Гамбурге находится одна из самых больших штаб-квартир компании Airbus, в которой трудятся 15 тысяч человек. Здесь есть центр подготовки технического персонала, центр кастомизации салонов, склад запчастей и лаборатории, в которых изучают новые технологии и возможности их внедрения, например 3D-печать. На местном заводе делают переднюю и заднюю секции фюзеляжа самого большого пассажирского самолета А380, секции A330 и A350, также здесь происходит финальная сборка всех моделей семейства A320 и A320neo. На производственную площадку привозят полностью готовые секции самолетов и соединяют между собой. Подобные линии финальной сборки есть также во французской Тулузе, китайском Тяньцзине и городе Мобил в американском штате Алабама.
Полный производственный цикл — от сборки первой детали до поставки готового лайнера заказчику — занимает около года.
Airbus А320 — самый популярный пассажирский узкофюзеляжный самолет в мире. Недавно этой модели исполнилось 30 лет, за это время все выпущенные самолеты А320 перевезли 12 миллиардов человек. А в 2010 году придумали модификацию A320neo с более эффективными двигателями, широким салоном и моделью крыльев, которая помогает улучшить аэродинамику. По крыльям как раз и можно узнать обновленную версию: на них есть шарклеты, то есть загнутые кверху законцовки. Авиакомпании эксплуатируют A320neo с 2015 года, но сейчас выпускают обе модификации – и старую, и новую.
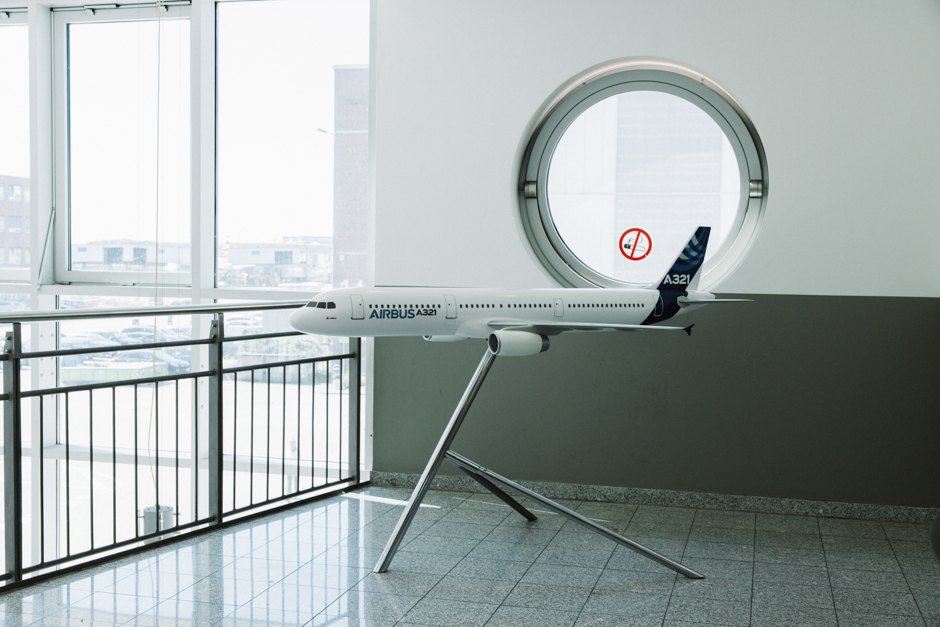
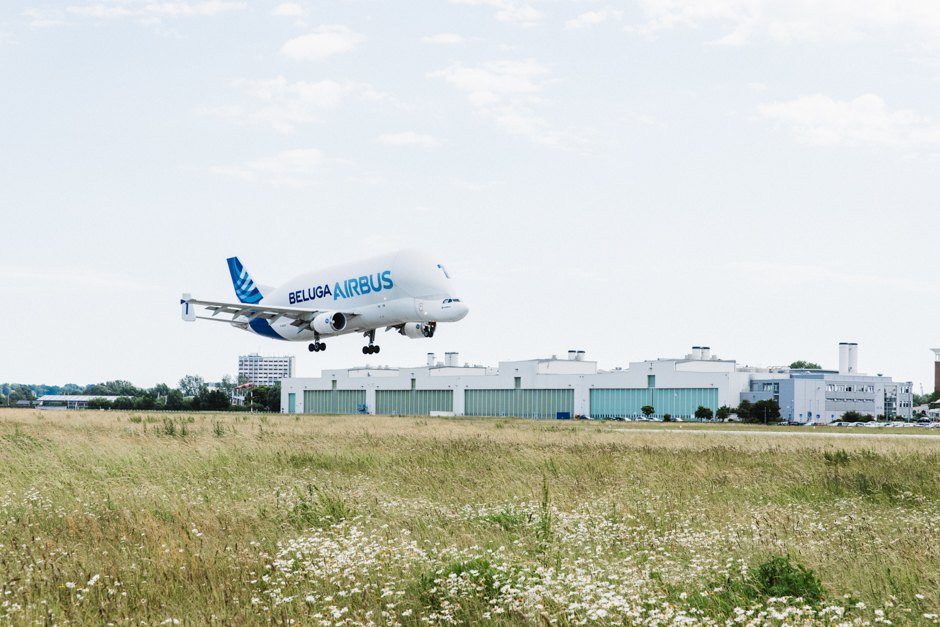
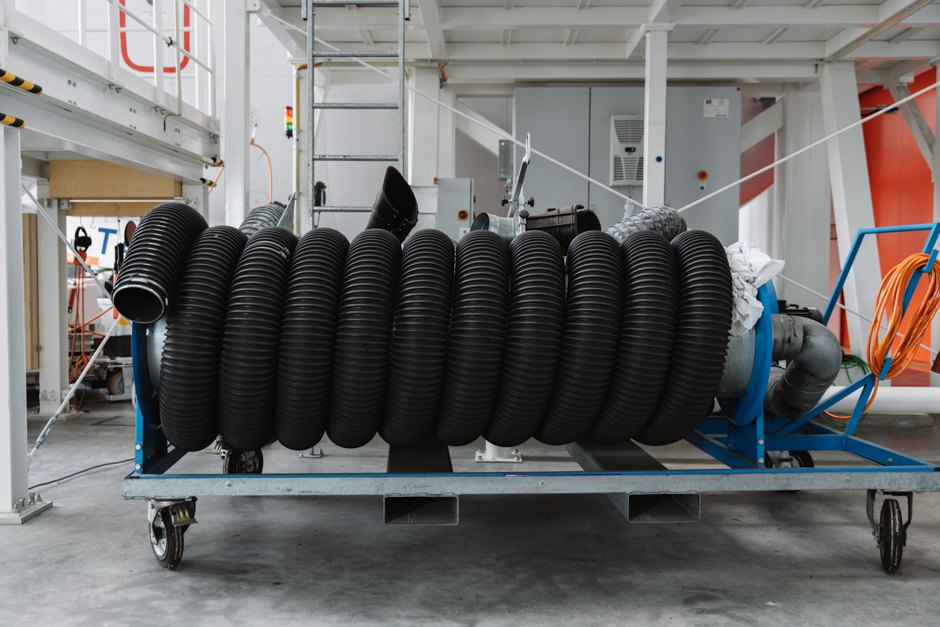
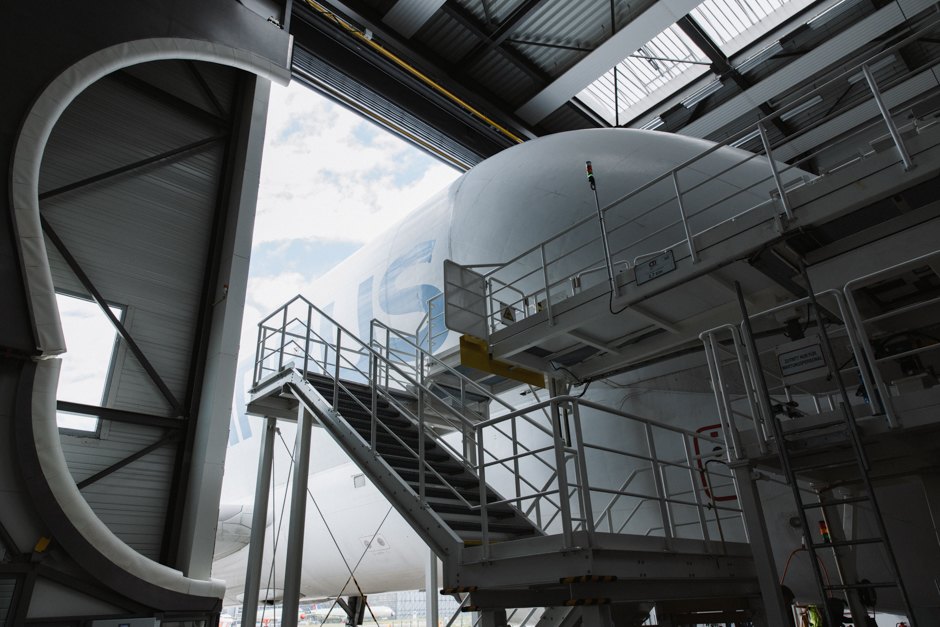
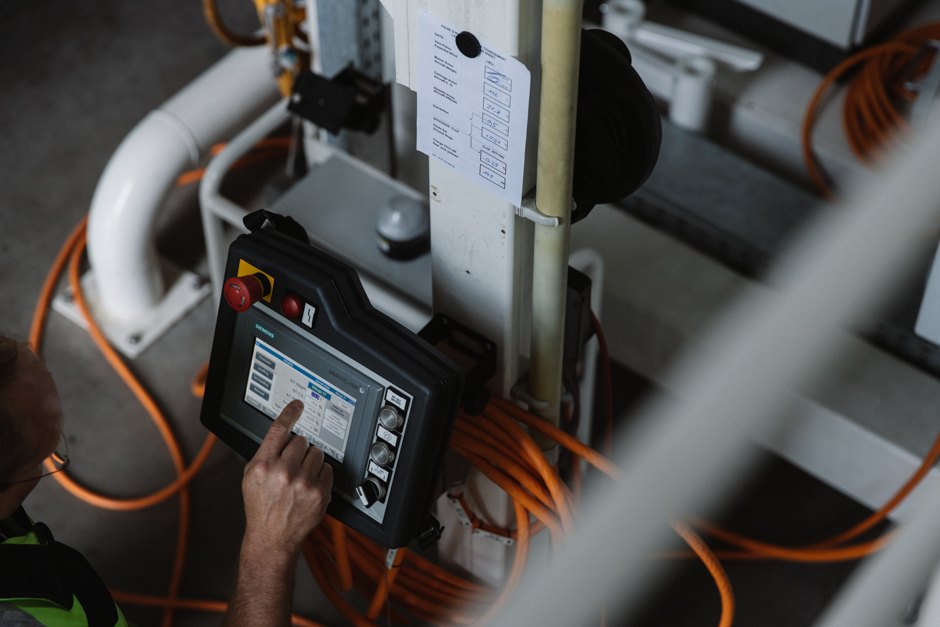
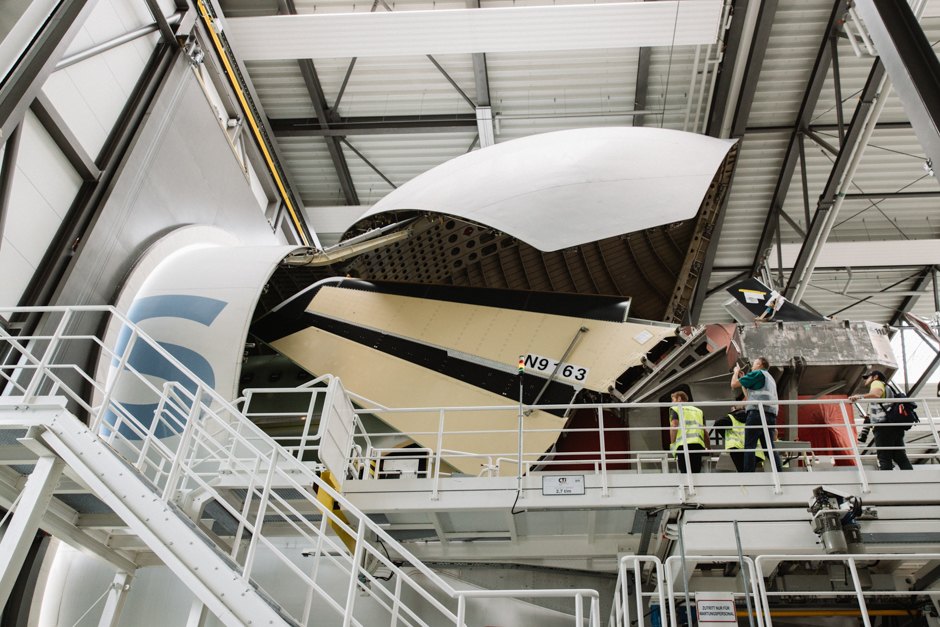
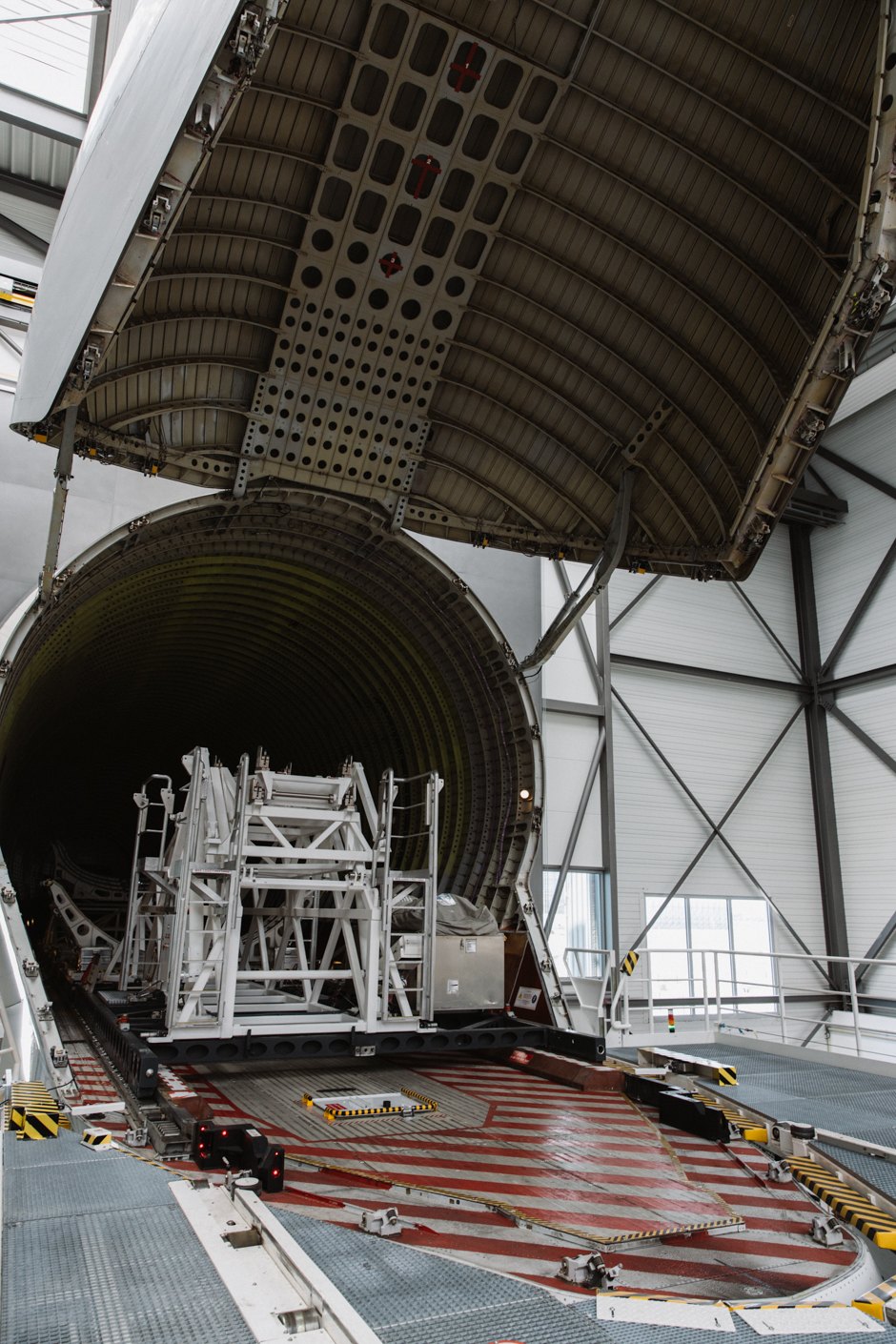
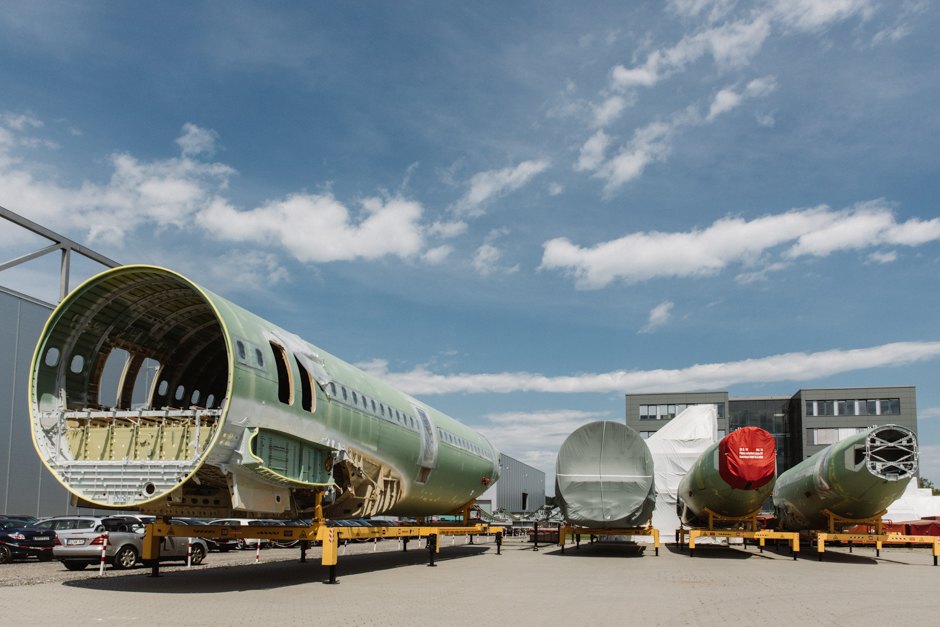
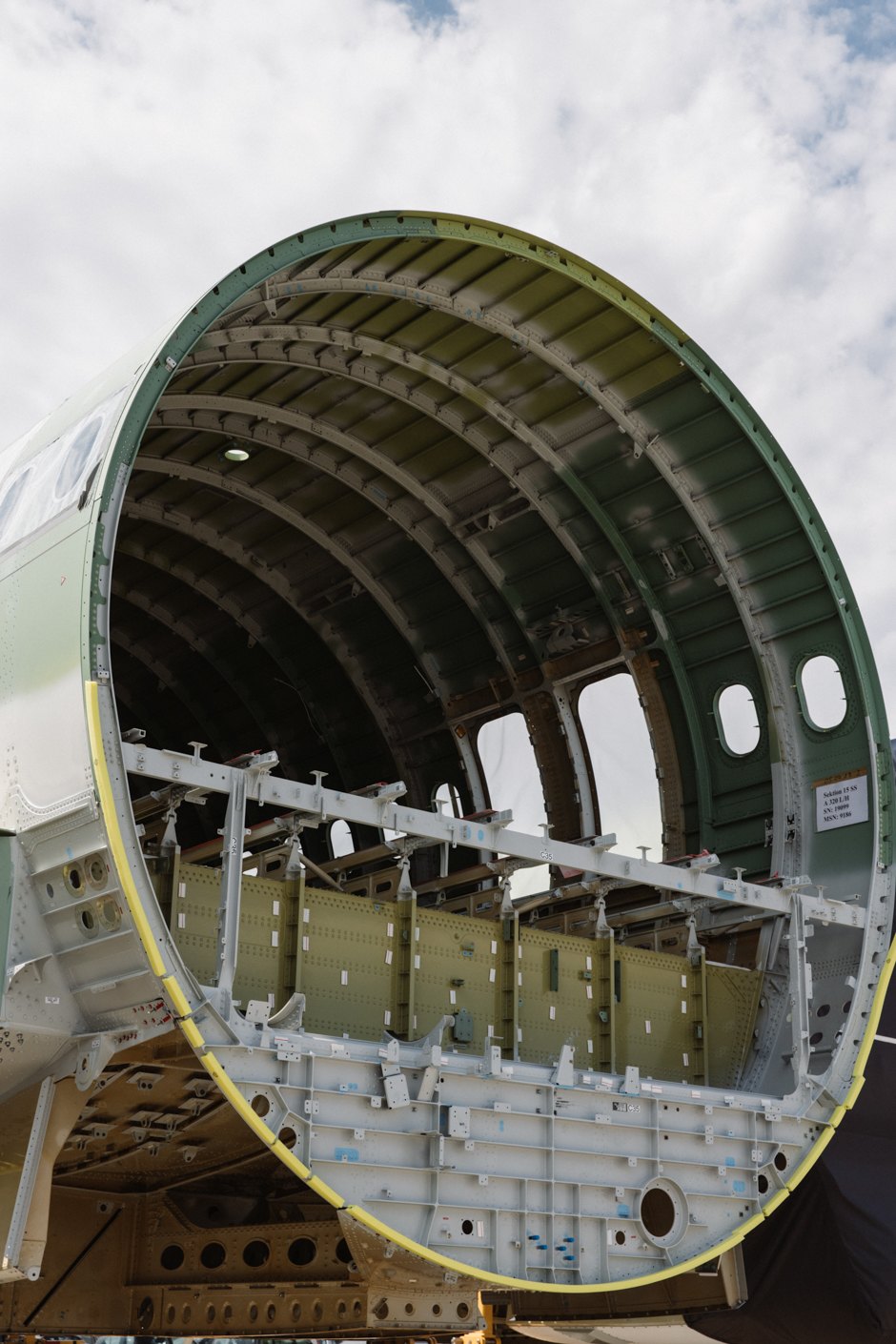
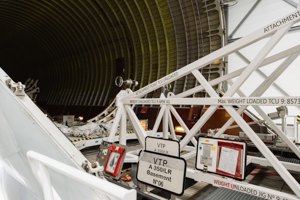
Каждый самолет А320 или A320neo состоит из 340 тысяч деталей, изделий и компонентов. Полный производственный цикл — от сборки первой детали до поставки готового лайнера заказчику — занимает около года. Все детали выпускают в разных странах, например, в Испании производят стабилизаторы, переднюю часть фюзеляжа делают во Франции, а крылья — в Великобритании.
Разрозненные части доставляют на линию финальной сборки на грузовом самолете Airbus Beluga, который был специально создан для транспортировки секций между заводами компании. Своей формой он действительно напоминает кита белуху, а перевозить может до 47 тонн. Объем грузового отсека Beluga — 1 400 кубических метров, туда помещается половина фюзеляжа А320. Сейчас пять таких самолетов выполняют порядка 65 рейсов в день, перевозя готовые части между заводами Airbus.
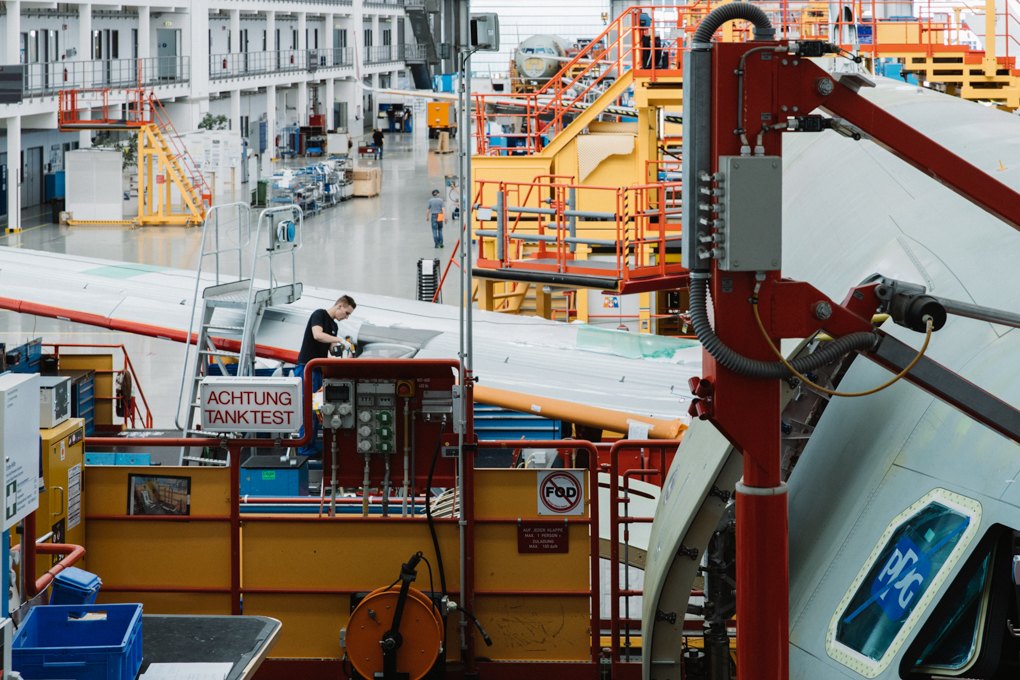
Линия сборки
Линия финальной сборки представляет собой огромный ангар, в котором размещено несколько станций для самолетов. В Гамбурге работают четыре линии финальной сборки, но роботы нового поколения используются только на одной из них. В Airbus объясняют, что, в отличие от производства автомобилей, на авиазаводе по-прежнему нужен ручной труд и доверить машинам многие процессы просто невозможно. Например, все 3 тысячи заклепок, при помощи которых скрепляют секции между собой, устанавливают рабочие, а не автоматы. В ангаре постоянно звучит музыка, которую выбирают сотрудники: считается, что она задает ритм и помогает трудовому процессу.
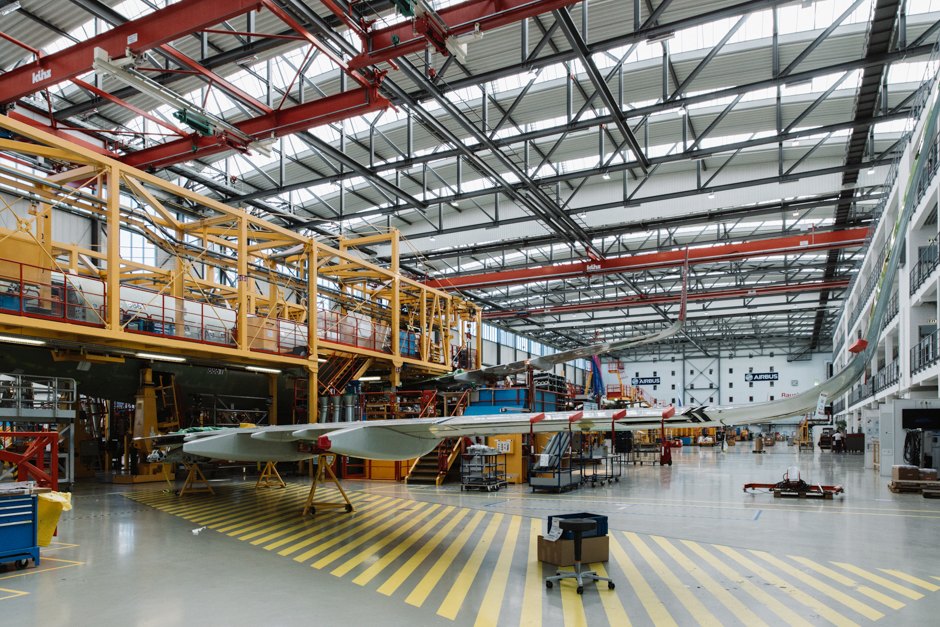
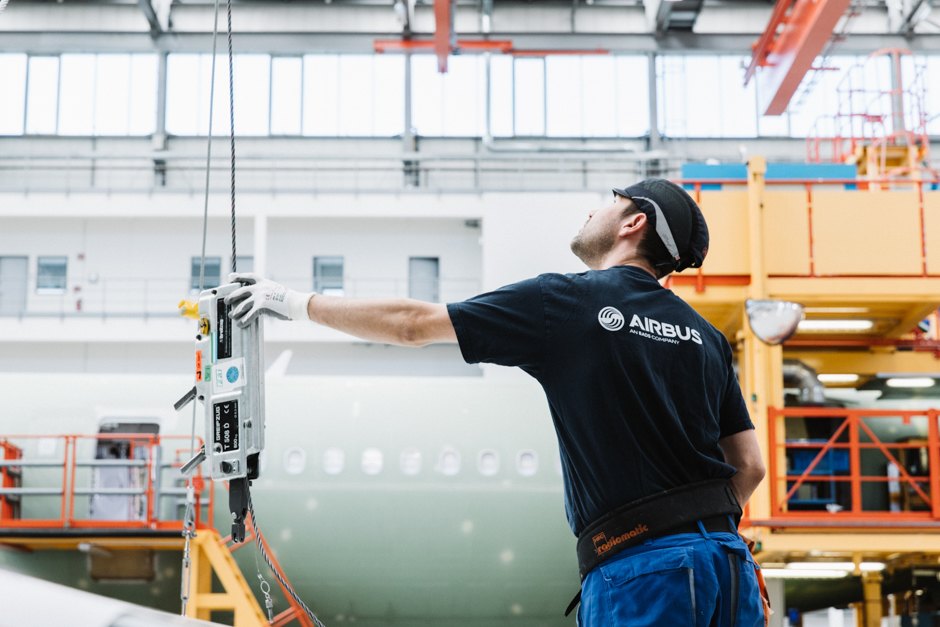
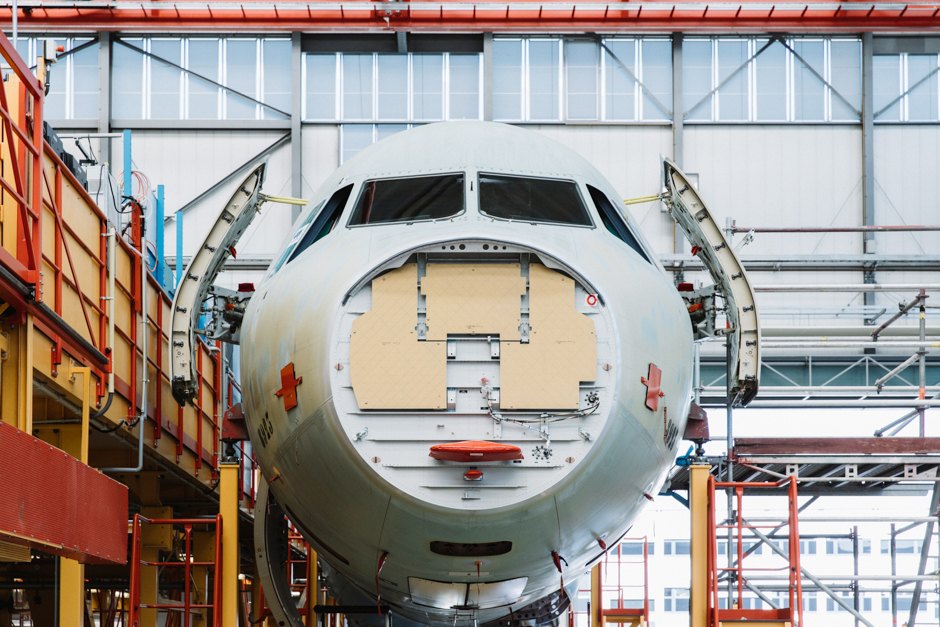
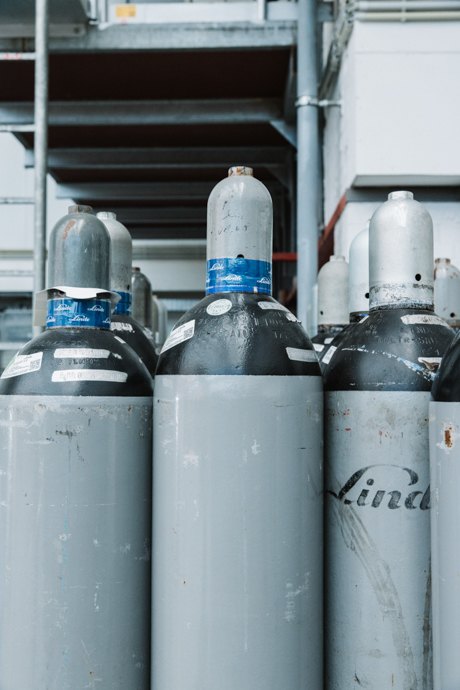
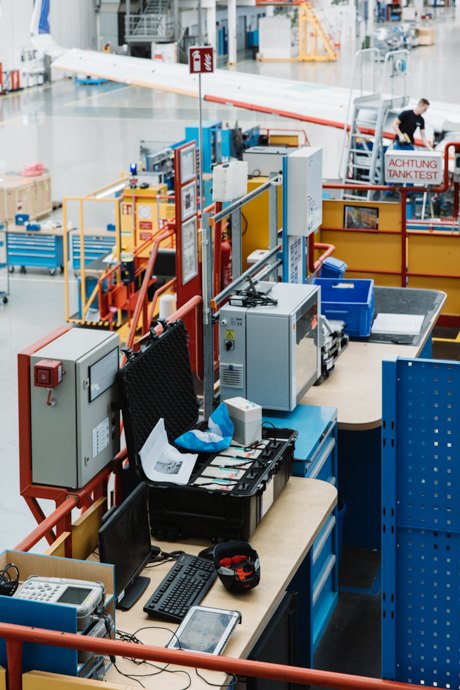
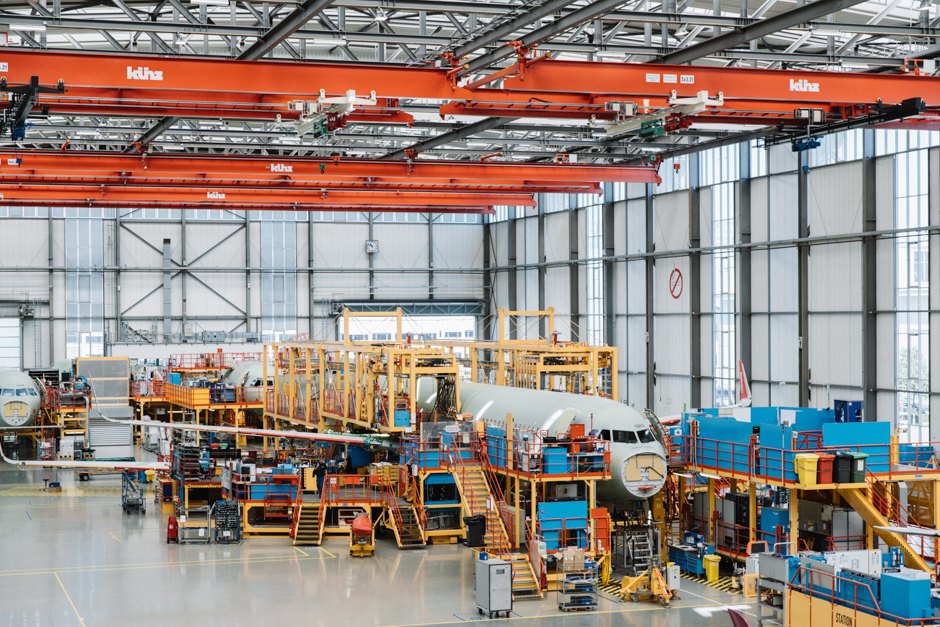
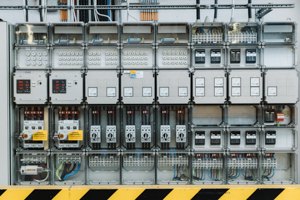
Линия финальной сборки поделена на четыре станции. На каждой из станций самолет проводит примерно два с половиной дня. Сначала соединяют переднюю и хвостовую части и скрепляют их как раз с помощью заклепок. Это не просто части корпуса, внутри уже установлена вся начинка из электрической проводки, звукоизоляция, системы кондиционирования и освещения. Пока у самолета нет шасси, перемещают части с помощью специальных кранов, закрепленных на потолке.
На следующей станции с помощью 1 200 заклепок к фюзеляжу прикрепляют крылья, а также устанавливают пилоны для подвески двигателей и шасси. Шасси — самый высоконагруженный элемент в самолете, потому для его изготовления используется прочный титан, в том числе российский. Дальше следует установка хвостового оперения — вертикальных и горизонтальных поверхностей, которые позволяют самолету поворачивать и устойчиво держаться в воздухе.
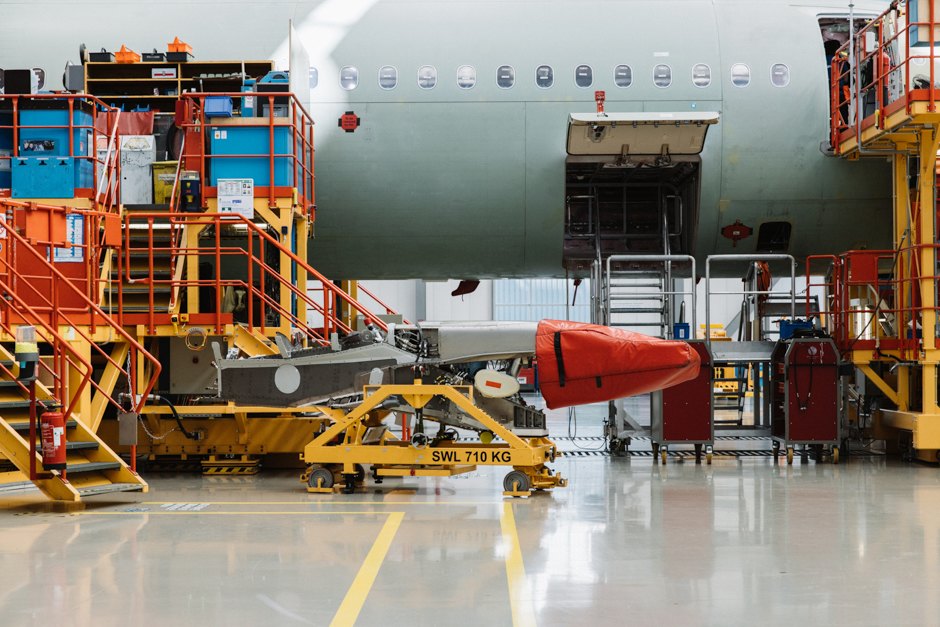
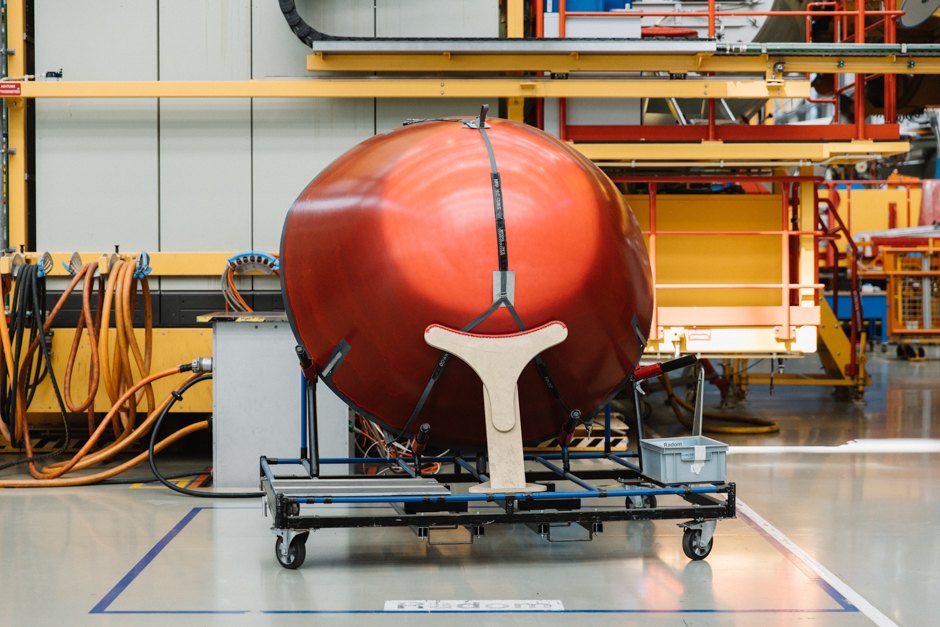
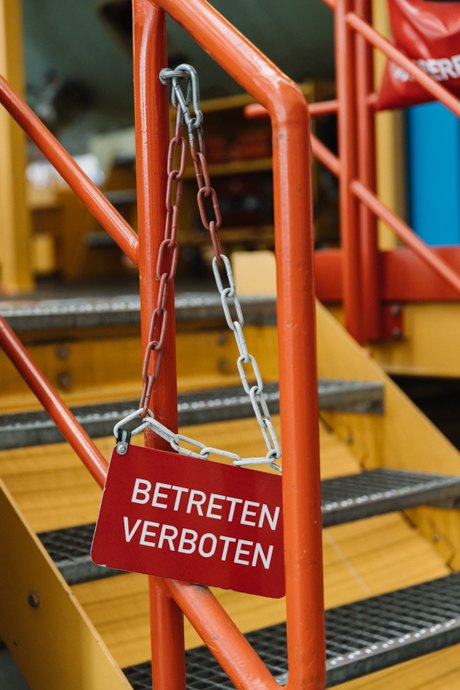
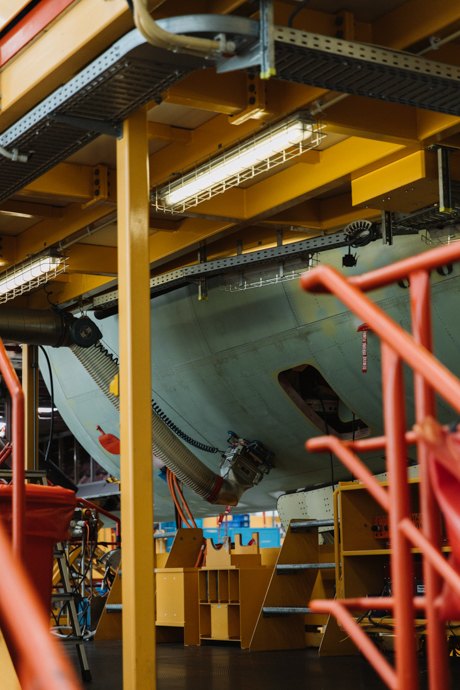
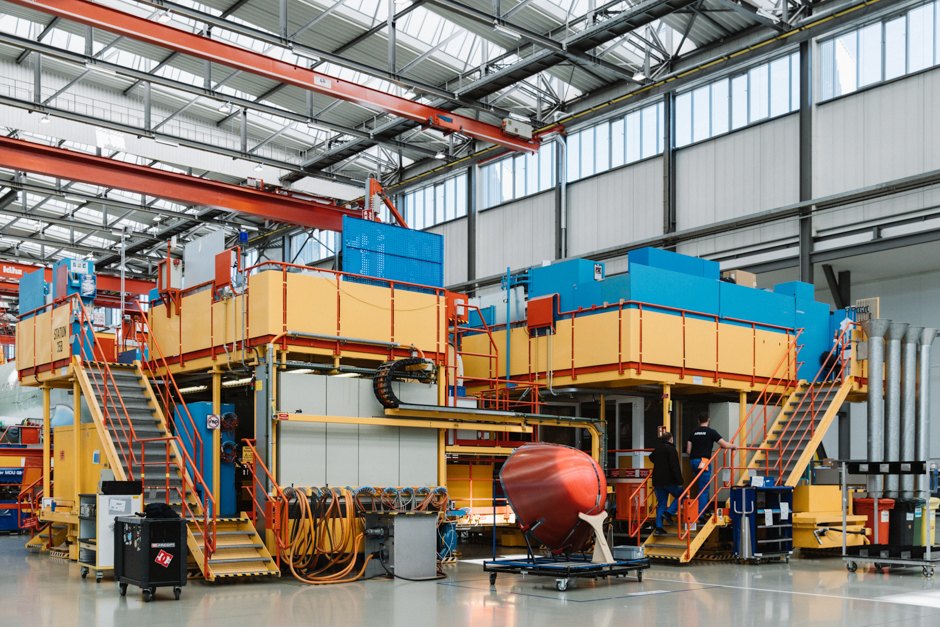
Все самолеты до того, как их покрасят в цвета авиакомпании, красноносые
Хвост и шарклеты, сделанные из композитных материалов, окрашены в цвета авиакомпании-заказчика заранее. А фюзеляж на стадии сборки остается зеленого цвета: его дает специальная антикоррозийная пропитка, которая защищает алюминий от ржавчины. Вообще все самолеты до того, как их покрасят в цвета авиакомпании, красноносые. Все радары, которые передают пилотам метеосводку, находятся именно в носу. Потому во время сборки эту часть закрывают красной пленкой, что должно напомнить сотрудникам о том, что с деталью нужно быть особенно осторожными.
На каждом промежуточном этапе все системы самолета тестируются, чтобы можно было сразу понять, как они работают. Но после сборки самолет проходит еще и финальную проверку на земле. Если все работает правильно, борт ждет покраска, установка двигателей и внутренняя отделка салона.
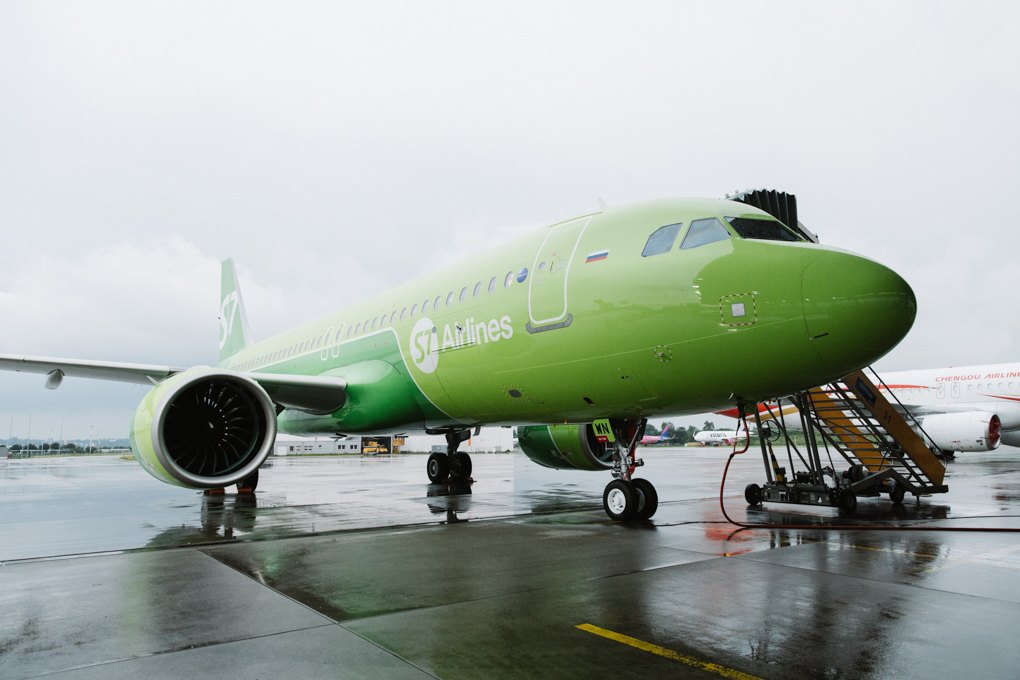
Внешний вид и интерьер
Из ангара, где находится линия сборки, самолет выкатывают и перевозят в покрасочный ангар. Иллюминаторы, шасси и крылья закрывают или заклеивают специальной пленкой, чтобы не испачкать. Все остальное рабочие красят вручную с помощью пульверизаторов. Когда краска высохнет, можно заниматься интерьером.
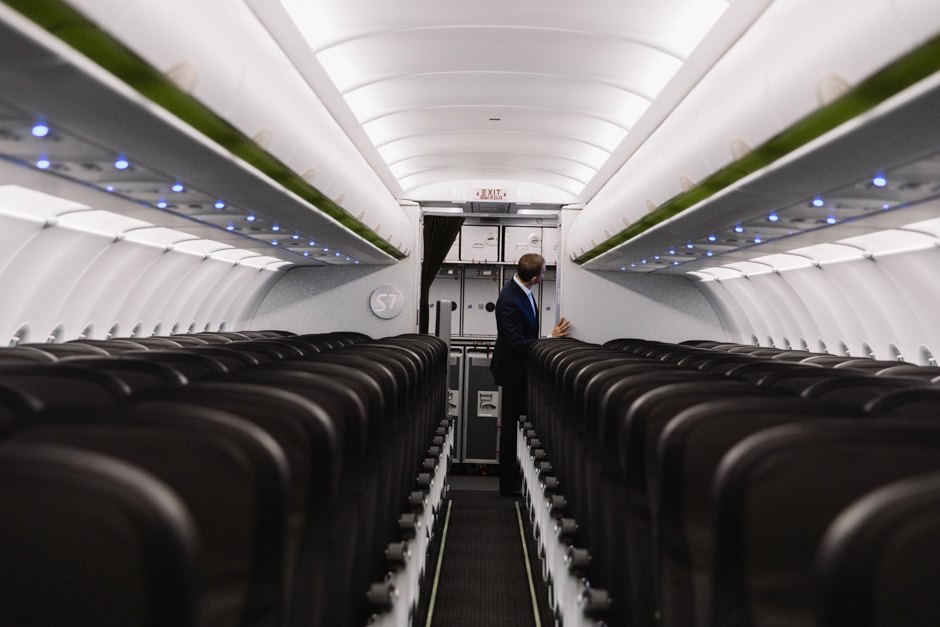
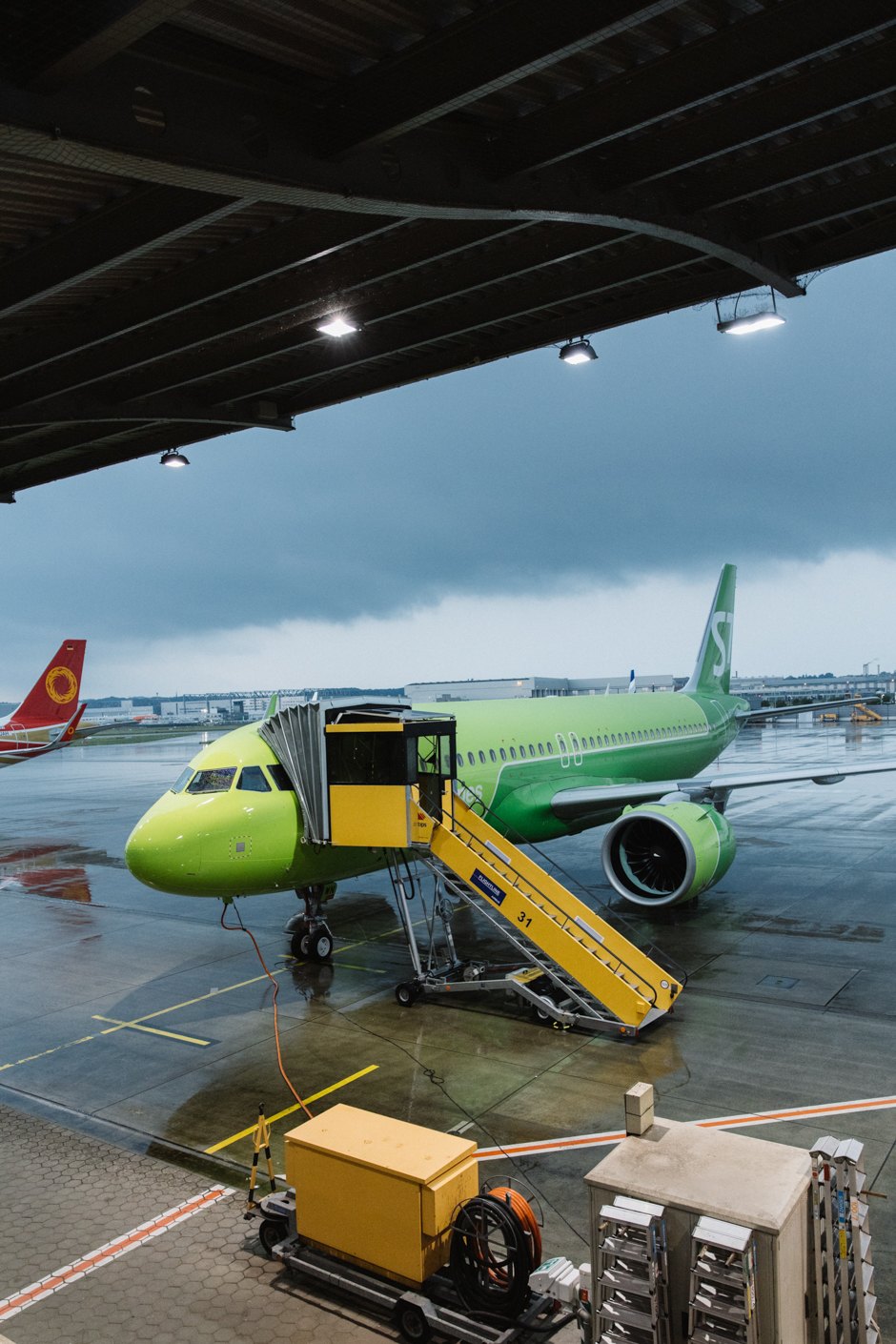
Кресло пилота обычно покрывают натуральной овчиной — такой материал не нагревается, не охлаждается и дает максимальный комфорт.
В А320 помещается от 96 до 200 пассажирских мест, все зависит от бизнес-модели и предпочтений заказчика. Шаг кресел и материал, которым будут обтянуты сиденья, тоже остаются на усмотрение клиента. Кстати, с точки зрения удобства пассажира тканевая обшивка выигрывает у кожзаменителя — сидеть на таких креслах не так жарко. Кресло пилота обычно покрывают натуральной овчиной — такой материал не нагревается, не охлаждается и дает максимальный комфорт.
Дальше самолет ждет еще несколько проверок уже не на земле, а в небе. Первый тестовый полет на нем совершают сотрудники завода Airbus, затем на новом лайнере поднимаются в воздух пилоты компании-заказчика. Теперь борт можно перегонять в аэропорт назначения и регистрировать.
Фотографии: Юлия Майорова / S7 Airlines
Чтобы прочитать целиком, купите подписку. Она открывает сразу три издания
месяц
год
Подписка предоставлена Redefine.media. Её можно оплатить российской или иностранной картой. Продлевается автоматически. Вы сможете отписаться в любой момент.
На связи The Village, это платный журнал. Чтобы читать нас, нужна подписка. Купите её, чтобы мы продолжали рассказывать вам эксклюзивные истории. Это не дороже, чем сходить в барбершоп.
The Village — это журнал о городах и жизни вопреки: про искусство, уличную политику, преодоление, травмы, протесты, панк и смелость оставаться собой. Получайте регулярные дайджесты The Village по событиям в Москве, Петербурге, Тбилиси, Ереване, Белграде, Стамбуле и других городах. Читайте наши репортажи, расследования и эксклюзивные свидетельства. Мир — есть все, что имеет место. Мы остаемся в нем с вами.