Производственный процесс: Как делают детское питание H&F посетил завод Nutricia и узнал, чем производство детского питания напоминает приготовление попкорна.
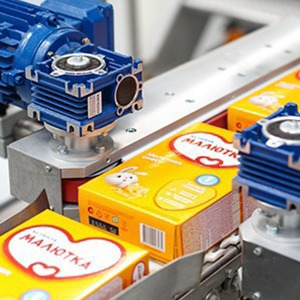
Компания Nutricia, специализирующаяся на производстве продуктов детского питания, была основана в 1896 году в голландском городке Зотермеер. Её основатель Мартинус ван дер Хаген впервые в мире получил право на производство специального молока для грудных детей, схожего по составу с материнским молоком. В 2007 году Nutricia вошла в состав подразделения детского питания Danone (Danone Nutricia Early Life Nutrition), и сейчас продукция компании продаётся более чем в 100 странах мира. В России Nutricia начала работать в 1994 году, а в 1995-м приобрела завод по производству детского питания в городе Истра и полностью его модернизировала. Теперь здесь производятся детские смеси и каши под брендом «Малютка».
Завод компании Nutricia
рАСПОЛОЖЕНИЕ
г. Истра
дАТА ОТКРЫТИЯ
1995 год
сОТРУДНИКИ
150 человек
производит
24 000 тонн
в год
Молочная основа приходит в «Нутрицию» из Ирландии. Она представляет собой сухой порошок, получившийся в результате смешивания молока, сыворотки и растительных масел. Смесь перемешивается, а затем распыляется с помощью форсунки. Под воздействием горячего воздуха из образовавшихся частиц выпаривается вода и в результате образуется порошок. Его упаковывают в биг-бэги, которые параллельно заполняются азотом, вытесняющим воздух. Это делается для того, чтобы внутри упаковки не происходил процесс окисления. Биг-бэг герметично закрывается, а затем на него надевают второй мешок — для транспортировки.
В таком же виде на завод попадает другое сырьё: витамины и минералы, которые доставляют с заводов в Нидерландах. «Нутриция» работает с зарубежными поставщиками, потому что российские фермеры пока не в состоянии предоставить сырьё надлежащего качества. Всё сырьё, поступающее на завод, проходит проверку в физико-химической и микробиологической лаборатории. Вторая — вынесена за пределы производства, опять же чтобы минимизировать риски.
Затем мешки с сырьём перемещаются в зону повышенного контроля. Для этого они проходят через специальный шлюз, в котором с них снимают транспортную упаковку и перекладывают с деревянных палет на пластиковые. Эта зона защищена от попадания любых вредоносных микроорганизмов. Местный воздух проходит через несколько стадий фильтрации. Очищенный воздух подаётся в помещение по тканевым рукавам, их легко снять и постирать. Всё оборудование и инструменты, проходящие через шлюз, дезинфицируют. Кроме того, зона повышенного контроля полностью свободна от воды. Моют и чистят здесь исключительно пылесосами. Все сотрудники завода ежедневно проходят медицинский осмотр и не допускаются к работе, если у них обнаруживают лёгкие признаки болезни. Те, кто управляет транспортом, также проходят тест на остатки алкоголя в крови.
У детского питания повышенные требования к первичной упаковке (той, что находится в непосредственном контакте с продуктом). Для этого всегда используется фольга, которая кроме своих барьерных свойств также хороша тем, что никак не взаимодействует с продуктом. Каждый новый поставщик проходит тест на качество и каждая партия материала тестируется на микробиологию.
Отсюда сырьё поднимают на четвёртый этаж в зону перемешивания. Там мешки вскрывают, раструб мешков дезинфицируют и соединяют с оборудованием, так что ингредиенты попадают в него без контакта с внешней средой. Компоненты дозируются с помощью высокоточных ячеек и затем попадают в блендер. При любом отклонении процесс автоматически останавливается. После блендера смесь попадает на сито с размером ячейки в 1,4 мм. Это барьер для возможных сторонних включений в продукте. Для этих же целей здесь стоит гигантский магнит. Дозирование, перемешивание и отсеивание происходит на разных этажах, то есть процесс выстроен вертикально, сверху вниз. Обычно для транспортировки продукта по трубам используется сжатый воздух, а здесь он падает под собственным весом.
Мука, прошедшая входной контроль, просеивается, а затем вместе с водой поступает в экструдер для обработки. Там при температуре 180 градусов и высоком давлении происходит разрыв молекулярной структуры муки. Этот процесс чем-то напоминает приготовление попкорна. Каждая частичка как бы взрывается и становится похожа на кукурузную палочку. Мука готовится, и параллельно благодаря высокой температуре умирает вся посторонняя микрофлора. Затем получившиеся пеллеты сушатся и перемалываются. Этот процесс позволяет сохранить многие питательные свойства, вкус и аромат продукта.
Перемешанный продукт проходит три этажа и попадает в зону упаковки. Расфасовка содержимого по пакетам происходит в среде азота. Азот — безопасный инертный газ, который вымещает кислород из пачки, создавая герметичные условия и предотвращая окисление. Процентное содержание кислорода в пачке составляет менее 2%. Такая упаковка позволяет хранить продукт в течение 18 месяцев.
Дальше пакеты взвешиваются и переходят в зону низкого контроля, где упаковываются в картонные коробки вместе с ложечками. Каждая коробка маркируется своим уникальным номером, в котором зашифрована полная информация о продукте. Затем коробки проходят через рентгеновскую установку, где проверяются на наличие посторонних включений. Если камера видит частичку, отличающуюся по плотности от остальных, пачка выбраковывается.
На заводе сейчас работает две параллельные линии смешивания и упаковки: одна только для молочных продуктов, другая — для продуктов, содержащих экструдированную муку.
Коробки с продуктом упаковывают в транспортные короба, которые затем автоматический робот-укладчик складывает на деревянные палеты. Сформированная палета заматывается в прозрачную защитную плёнку, маркируется и поступает на склад в зону карантина. В течение пяти дней продукт проходит финальные проверки. Для этого из каждой партии отбираются пробы и отправляются в лабораторию. Только после этого продукт покидает зону карантина и отправляется в магазины.
Фотографии: Иван Гущин
Чтобы прочитать целиком, купите подписку. Она открывает сразу три издания
месяц
год
Подписка предоставлена Redefine.media. Её можно оплатить российской или иностранной картой. Продлевается автоматически. Вы сможете отписаться в любой момент.
На связи The Village, это платный журнал. Чтобы читать нас, нужна подписка. Купите её, чтобы мы продолжали рассказывать вам эксклюзивные истории. Это не дороже, чем сходить в барбершоп.
The Village — это журнал о городах и жизни вопреки: про искусство, уличную политику, преодоление, травмы, протесты, панк и смелость оставаться собой. Получайте регулярные дайджесты The Village по событиям в Москве, Петербурге, Тбилиси, Ереване, Белграде, Стамбуле и других городах. Читайте наши репортажи, расследования и эксклюзивные свидетельства. Мир — есть все, что имеет место. Мы остаемся в нем с вами.